Non-Contact Flow Meters in Continuous Processing & Single-Use Applications
SONOFLOW® CO.55 as Component to Fulfil PAT-Requirements in Biopharma Production
The ever-running trend for supporting closed operations with flexible single-use solutions (SUS) designed for continuous processing reflects a paradigm shift in biopharmaceutical facility design. The combination of SUS and continuous bioprocessing is changing the industry’s conception of itself, having a significant impact on facility design by offering a smaller equipment footprint and substantially lower cleaning requirements. The implementation of a continuous process monitoring guarantees to keep process stability and to raise overall efficiency.
Benefit from Our Clamp-On Flow Meters
More Information about Ultrasonic Flow Meters
Do you have any questions?
Feel free to contact us! We will be happy to help you.
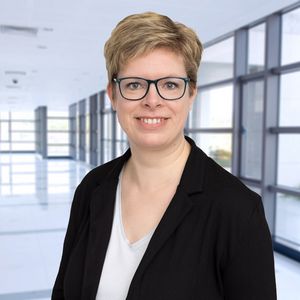